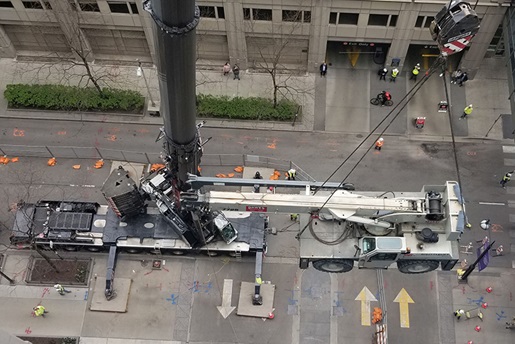
It’s not every day that a carry deck crane gets to play the hero and come to the rescue. As the lift industry has evolved to showcase ever-larger cranes with longer reach and higher capacities, smaller equipment can sometimes seem pushed to the margins.
But when Northwestern Memorial Hospital in downtown Chicago had a three-story “connecting link” project with special circumstances, it turned out a 25-ton carry deck crane was the perfect piece of equipment for the job. Although the solution is elegant in its simplicity, getting there took the combined efforts of some of the most respected construction, engineering, and heavy lift companies in the Chicago area. Power Construction was general contractor, Chicago Steel the steel erector, Dearborn Companies acted as construction engineering and heavy lift consultant, cranes were provided by Central Contractors Service, a member of the ALL Family of Companies, and Sterling Lumber provided crane mats
The project, joining the 10th through 13th floors, was especially delicate because the lift equipment selected would need to be positioned atop an eight-story connector between the Galter and Feinberg Pavilions in the medical center complex. The regular daily work functions of the hospital would continue throughout the job, ratcheting up already critical safety concerns (the floor directly under the work zone remained evacuated during the project).
Dearborn Companies worked closely with Central Contractors Service to develop specifications the chosen crane would have to fulfill.
“We couldn’t place a large crane on the street below and use its longer boom to reach the walkways,” said Michael T. Walsh, president of Dearborn Engineers & Constructors. “The reason was twofold: we couldn’t shut down the nearby roadway for the three-month duration of the project, and the hospital didn’t want us blocking the patient entrance for that long, either.”
That meant a crane was going to have to be placed on the eight-story roof, where it could then help construct the walkways to be placed between the ninth through twelfth floors of two taller towers in the hospital complex.
But what kind of crane? A mini crane was certainly small enough, but it didn’t have the capacity to handle the steel, glass curtainwall, and buckets of concrete needed to construct the walkways. A derrick would have been costly and taken up too much space on the roof. So, Central Contractors Service recommended using its all-terrain crane to lift and set the carry deck crane on the roof.
Walsh credits Central’s sales manager, Paul Urbanski, for coming up with a perfect solution.
“Paul might be the most knowledgeable crane guy in the country, not just Chicago,” said Walsh. “His opinion carries a lot of weight.”
Central specified a Manitowoc Shuttlelift CD7725 with a 71-foot, four-section power boom and a capacity of 25 tons. To lift the Shuttlelift into place, Central provided a 550-USt Liebherr LTM 1450-8.1 all-terrain crane with 279 feet of main boom. In addition to lifting the carry deck crane, the Liebherr was also tasked with lifting the project’s larger steel beams and columns to the roof. The Shuttlelift set the structural steel while also hoisting curtainwall glass and concrete from street level to the roof and placing it.
Walsh’s team at Dearborn specializes in stabilization design for heavy lift operations and rigging. They started by laser-scanning the roof and structural elements below the work area, and structurally evaluated the building before developing a plan to use three layers of CLT “access” mats on the roof to evenly distribute load. It took a total of 78 mats to cover the 3,500 square foot roof in triplicate.
Next, they plotted the six precise positions where the carry deck could be placed in the course of its work. These positions, clearly marked in paint, assured that three outriggers were always on a support beam or foundational column. “No swing” exclusion zones were engineered and maintained over the fourth outrigger. Two positions were used to hoist material from the street, and four were for lifting and setting material on the under-construction walkways.
Over the three-month project, the carry deck set 100,000 pounds of steel, lifted glass for the curtainwall in 3,000-pound pallets, and hoisted 100 cubic yards of concrete—done a half-yard at a time to minimize loading on the existing building structure.
General contractor Power Construction maintained monitoring of roof deflection to make sure the carry deck was operating safely. They discovered that, even during the heaviest loads, the roof deflected a scant quarter-inch.
The result proved that the meticulous planning paid off—and that Central made the right call in recommending the Manitowoc Shuttlelift CD7725 for the job.
“When you’ve got the proper knowledge and expertise behind it, even a small tool can make a big impact,” said Walsh.