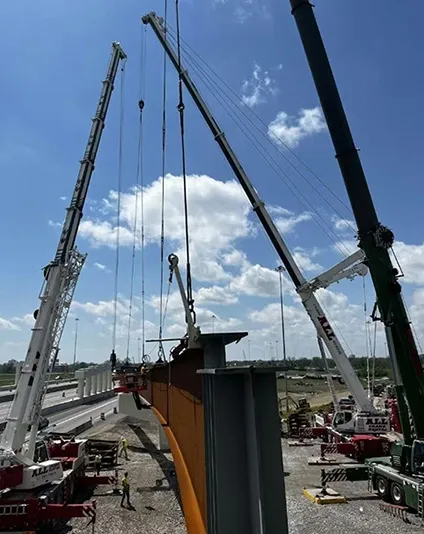
The renovation of Columbus’ I-70/I-270 interchange is rolling on with a phase that relies on four cranes acting in tandem to accomplish girder lifts. ALL Crane Rental Corp. of Columbus, a member of the ALL Family of Companies, is providing all-terrain (AT) cranes ranging in capacity from 50 tons all the way up to 770 tons for the work.
Dan Lewis, project manager for Youngstown Bridge, LLC, ALL’s customer, describes the intricacy of four cranes working together to achieve setting a spliced girder. There are essentially three sequences that need to happen: 1) lifting two girder pieces so they can be spliced in mid-air; 2) repeating this process with two additional pieces; and 3) adding cross frames in between to create stability.
For most lift sequences, ALL provided the following cranes: Liebherr LTM 1650-8.1 (770 USt), Liebherr LTM 1300-6.3 (360 USt), Liebherr LTM 1090-4.2 (110 USt), and Liebherr LTM 1060-3.1 (50 USt). For some lifts, a Liebherr LTM 1350-6.1 (400 USt) was swapped in for the 360-ton crane.
Rich Randall, general manager of ALL Crane Rental of Columbus, credited his sister branches for helping to gather such an impressive line-up of machines for a single project. “In addition to our own yard, we pulled cranes from Cleveland, the ALL Family’s headquarters location, and Jeffers Crane Service in Toledo,” said Randall. “It’s always a team effort, but especially with a project this large. Just the logistics of getting everything delivered on time is a testament to ALL’s logistics team and Ryan Flack here in Columbus.” Randall also praises sales rep Chris Kirk for his work in bringing the project together.
Lewis describes the lift process as requiring precision from everyone involved.
“The 770-ton crane picks the girder closer to the bridge pier, as it is usually the heavier of the pieces, while the 360-ton crane picks the second piece,” said Lewis. “These two cranes then hold their pieces while they are spliced in mid-air and set on the pier cap.” At this point the work isn’t even half-finished. Once splices are complete, the 110-ton crane holds the set so they won’t fall over (a risk with curved girders) as the two larger cranes repeat their process with two new girder pieces. Once these two new pieces are spliced, the 50-ton crane is used to fly in cross frames. Once the cross frames have joined the curved sections, the girders are stable enough for the cranes to release.
“We’re dealing with boom length in excess of 180 feet,” said Lewis. “This is because the rigging for each piece is 100 feet long – necessary to pick the curved girders at the appropriate center of gravity and then maintain a plumb girder to mate with the adjacent piece.”
This phase of the interchange project, referred to as “Ramp A-2,” involves setting 75 individual girder pieces with lengths ranging from 60 feet to 140 feet and total weight of nearly 5.5 million pounds. Work is being performed at night, with a goal of completing the splicing and cross-framing of four pieces each work night. Time is precious, because the cranes need to be moved to a nearby laydown yard at the end of each night so daytime traffic is not impacted. The necessary crane setup at the start of work and removal at the end takes up four hours of each work period.
Work on the interchange ramp will continue through June. Selly and Sands is the general contractor for the project.